AT A GLANCE
- Custom Solution
- Space Constraint
- Non-Standard Panel Sizes
- Accurate, Automated Repairs
- Reduced Downtime
Need
Modernizing Repair Operations
Timber Products, a leading manufacturer of sustainable wood products, sought to modernize their plywood panel repair process by transitioning from manual repairs to an automated solution. The challenge? Fitting an advanced system into a small, existing footprint while accommodating non-standard panel sizes. To tackle this, Timber Products partnered with us — and alongside 7robotics and Argos Solutions, we designed, engineered, and built a custom Robotic Panel Repair Line to streamline production and improve efficiency.
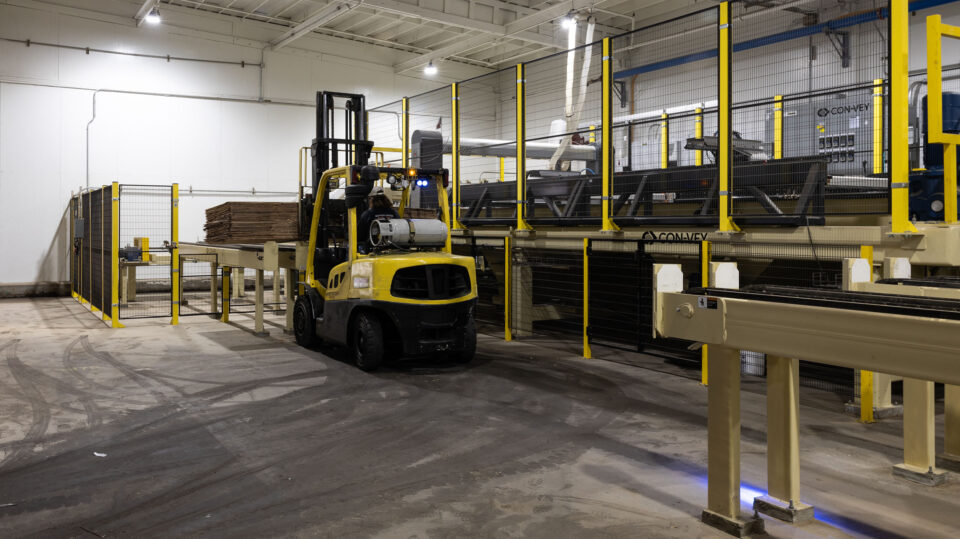
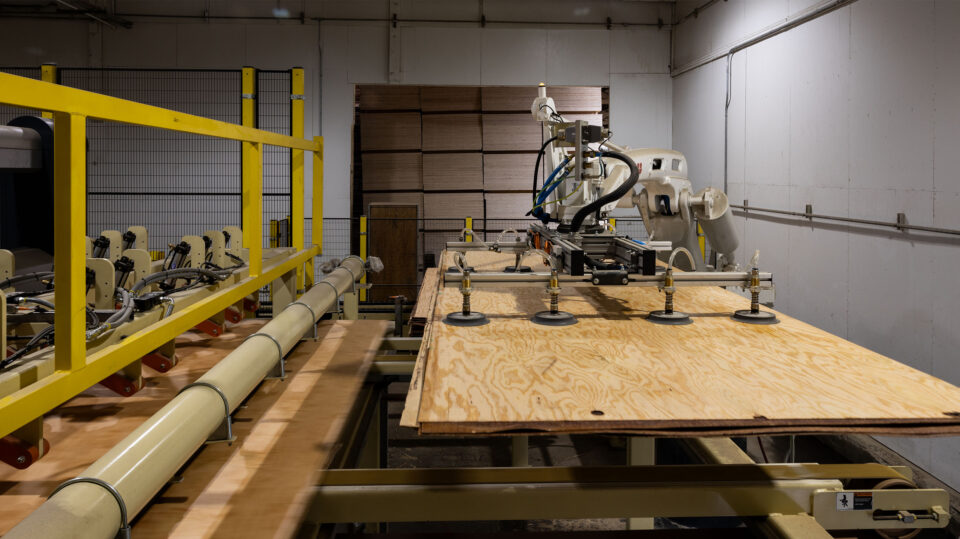
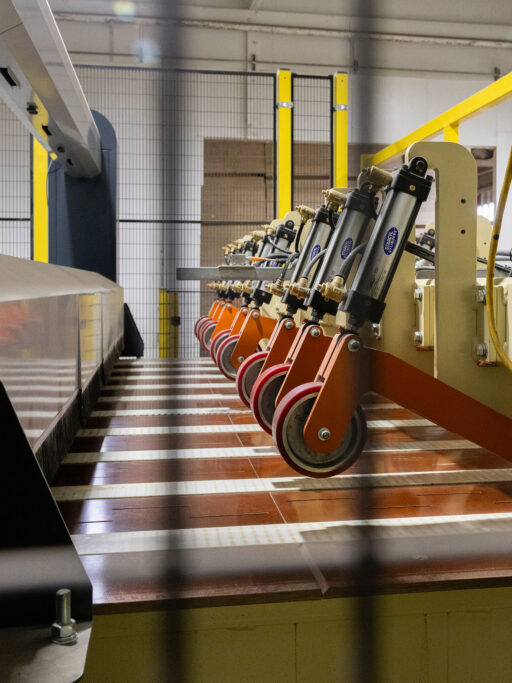
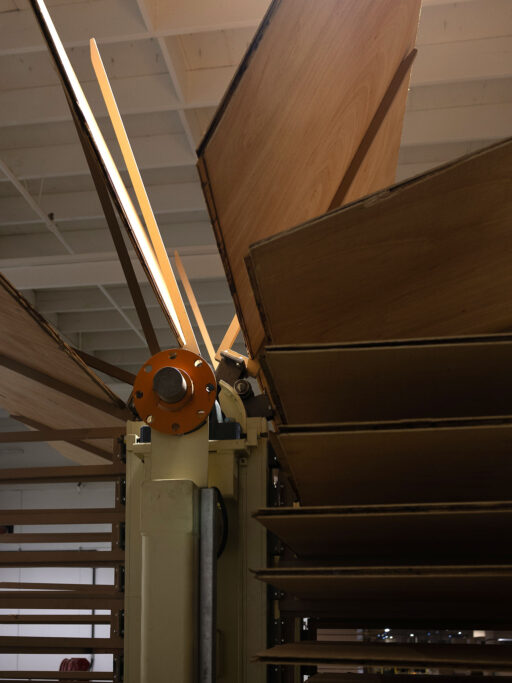
Con-Vey is in our backyard; they are a great, reliable team and do things that are outside our scope of work. We’ve been wanting to take this technological step for awhile, and Con-Vey was an integral part of our decision to proceed with it. This panel repair line was a home run.
Ben Ralph
Engineering Manager / Timber Products
solution
Engineering a Compact Solution for Big Results
Con-Vey’s proven expertise in automated panel repair systems made us the natural choice for the project. As panel repairs remain a labor-intensive area with rapidly evolving technology, we needed to deliver a solution that would future-proof operations while fitting within a constrained space. Working closely with Timber Products, we converted a small building into a suitable home for this state-of-the-art repair line. Their proximity in Southern Oregon facilitated frequent collaboration, ensuring the solution was tailored to meet Timber Products’ needs.
Con-Vey is very open to sharing the risks of trying a new way. They are easy to work with and that flexibility allows us to work on those R&D ideas.
REsult
Seamless Integration, Reduced Downtime, and New Opportunities
Con-Vey played a critical role as the project’s integrator, addressing space constraints while coordinating the multiple components of the system. We were able to work out all bugs before Argos installed their equipment — making for a smooth transition with minimal disruption. According to Ben, unlike many projects where startups lag, this one “wasn’t zero to forty percent, it was more like zero to eighty from the get-go,” resulting in smooth operations from day one. With this automated line in place, Timber Products not only boosted efficiency but also freed up employees to move into new roles.
The success of this panel repair line continues our confidence in future projects. We’ve really enjoyed working with the Con-Vey team.
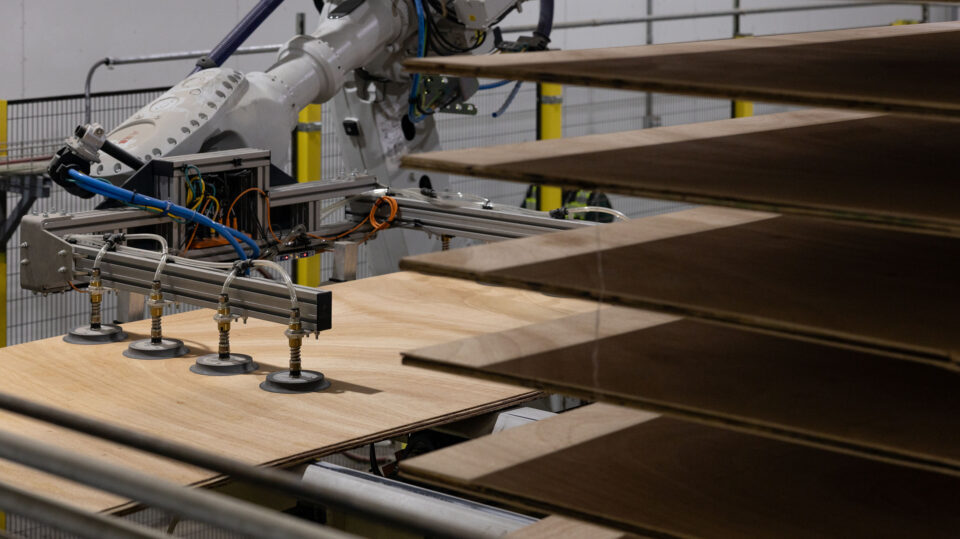
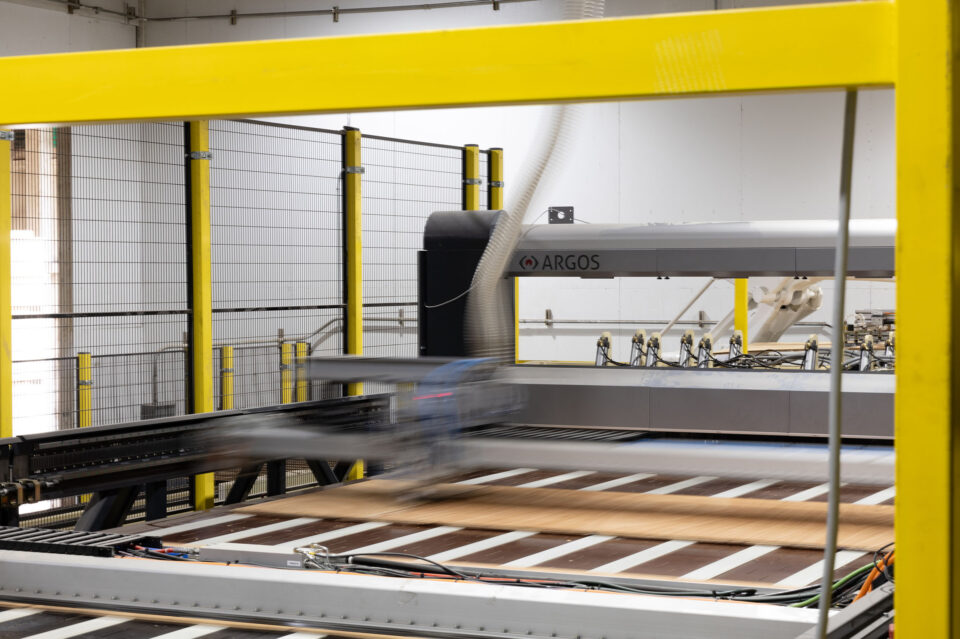
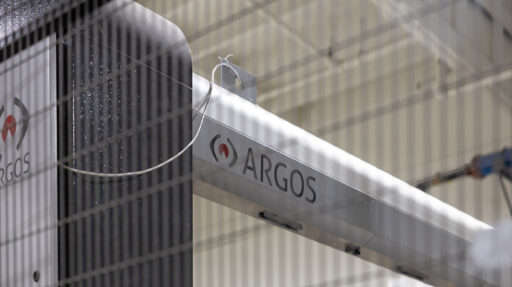
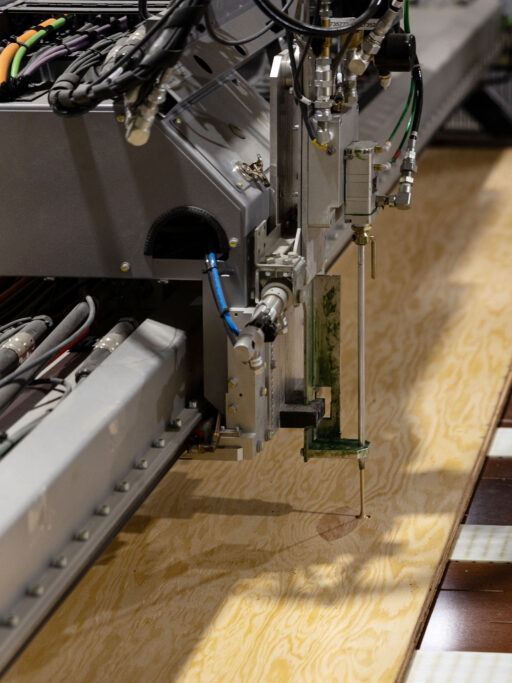