AT A GLANCE
- In-Line Repair Process
- Labor-Saving Automation
- Reduced Chemical Waste
- Precision Edge Sealing and Repair
Need
Cutting Costs and Labor — Without Cutting Corners
At their facility in Chopin, Louisiana, RoyOMartin faced a familiar but costly challenge: manual panel repair. Traditionally, every panel defect had to be routed and filled by hand — a slow, labor-intensive process that relied on a large, dedicated workforce. When Covid-19 strained labor availability even further, it became clear that a better system was needed.
However, the solution required more than automation — it called for a reimagining of the repair process itself. While standard repair lines work on rough, untrimmed panels, they sought a system that could handle precision repairs after panels were cut to size. To bring this vision to life, they once again turned to Con-Vey, their trusted partner for complex, custom-engineered solutions.
It was both cost- and people-driven. The price of the chemical we use on that line had increased tremendously. On top of that, it was a very labor-intensive job, and we were seeing a lot of turnover. So having somebody monitor the process versus actually doing it is a big deal out here.
Jeremy Burford
VP of Plywood / RoyOMartin
solution
Precision Repairs with Real-Time Curing
Changing this sequence — sawing, repairing, then sanding — required unprecedented ingenuity. The key challenge? Timing. At room temperature, repair material needs 40 seconds to harden before it can be sanded — a difficult ask for a continuous production line.
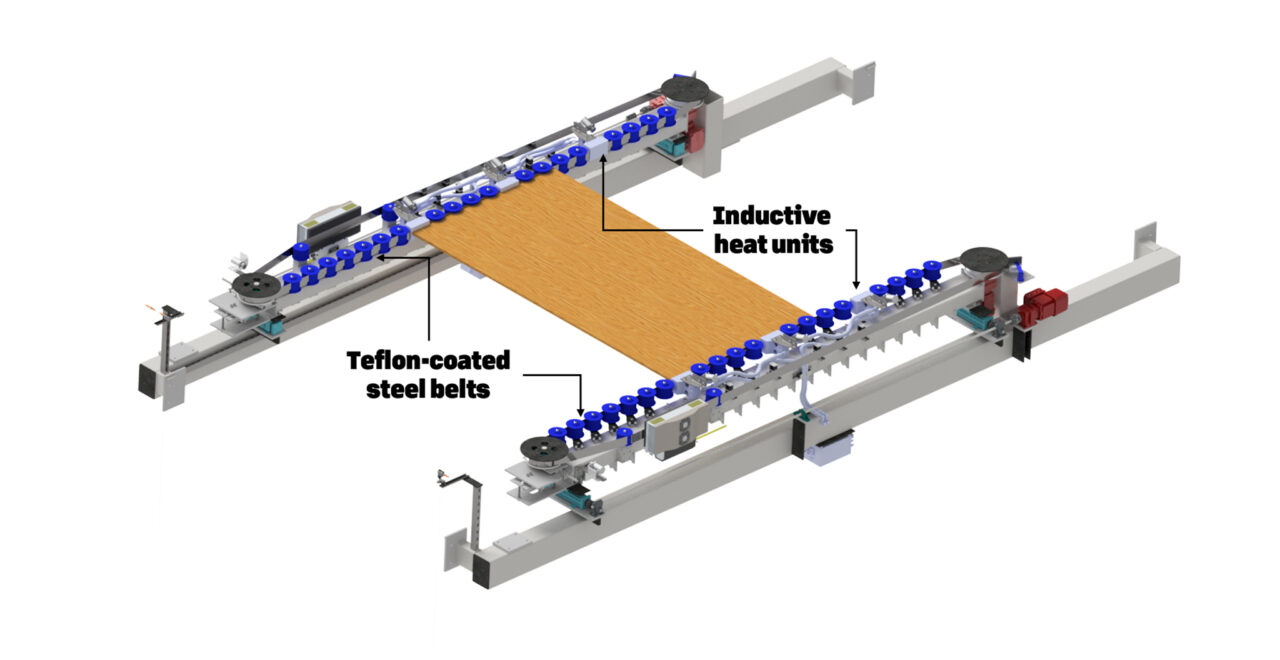
To meet this challenge, Con-Vey developed a patent-pending edge-damming system, the first of its kind at RoyOMartin. The system uses a Teflon-coated steel belt to form a precise seal along the edges of routed areas. As defects are filled, an inductive heating unit applies controlled heat to initiating curing. This direct, in-line process increases efficiency while reducing chemical waste and operator labor — all while keeping production in continuous flow.

Repairing to the end of the panel poses challenges, because the chemical needs to get hard enough that it won’t run out of the defect that’s been removed. Con-Vey said they could figure it out, and we’ve never had to do it any other way, so I’d say it was a success.
REsult
Shaping the Future of Plywood Production
By shifting from manual to automated panel repair, RoyOMartin has seen higher throughput, lower costs, and safer, more sustainable roles for employees. The system also reduced material waste, thanks to more precise routing and filling techniques. This marks a major step in their larger push toward automation, and the impact was clear: they ordered a second edge-damming system not long after the first went live.
We’ve reduced costs on the line, we’ve reduced turnover, we’ve improved on grades, we’re meeting the panel throughput that we thought we would. The project has been a huge success. We’re very appreciative that Con-Vey took this risk with us. I wouldn’t hesitate to do any other project with their team.
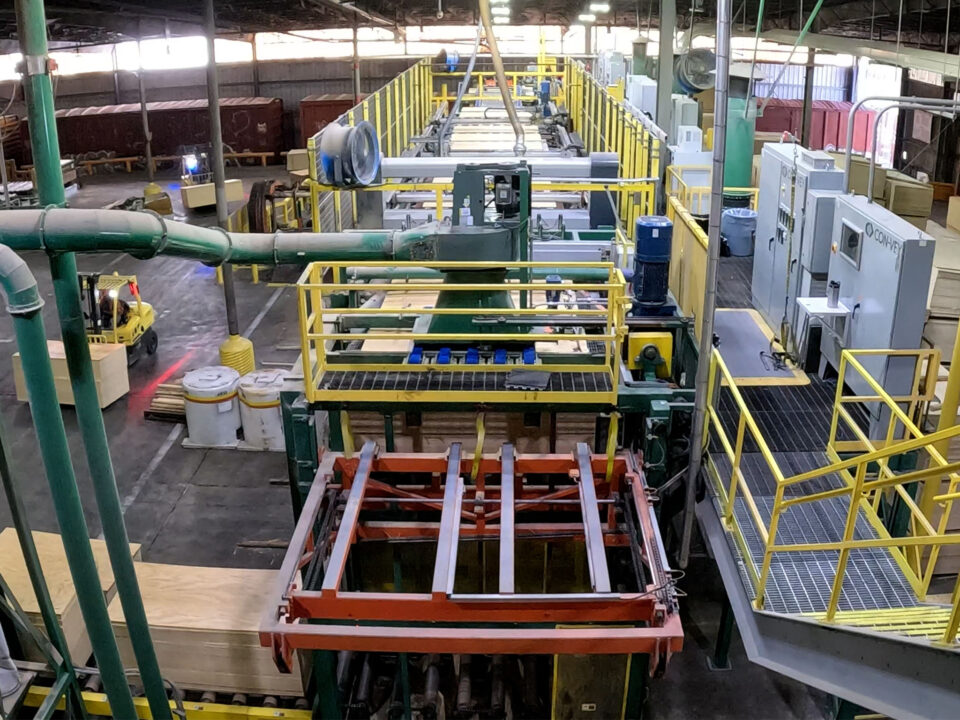
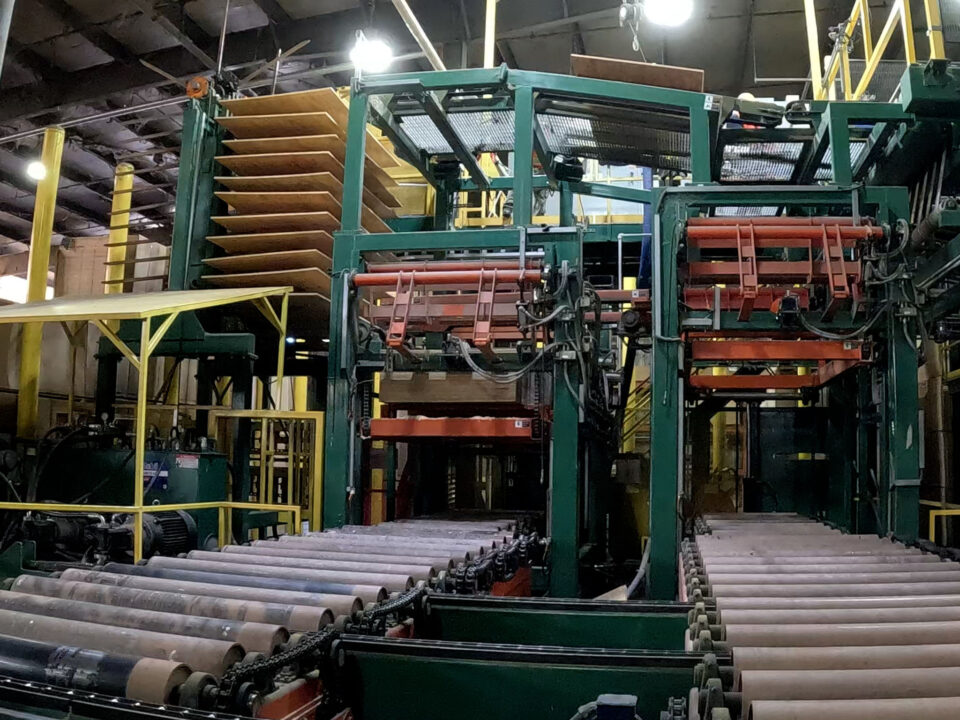
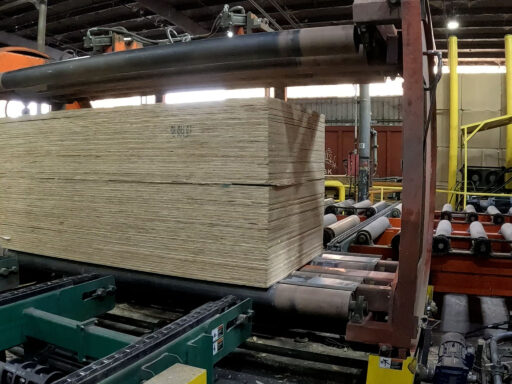
